Electro Fusion (EF) Welding of PE Pipes & Fittings
Electrofusion jointing or welding aka EFW melts and fuses the PE pipe & fittings using an electrical resistance element in the socket of the fitting. Electrofusion welding is an effortless joining method for PE pipes in circumstances where butt fusion welding is not practicable, where valves, elbows, and tees must be added. Prefabricated fittings are used, incorporating an electrical heating coil that melts the plastic of both the fitting and the pipe, causing them to fuse. The benefits include safety, connectivity at high speed, and cleanliness. But on the other hand, the limitation of this method is the high cost and maximum diameter of the pipe that can be connected. Electrofusion fittings due to their high coefficient of reliability are commonly used in irrigation networks for polyethylene pipes and are economical for pipes of 20 to 250 mm in diameter. EF joining method can also be used for joining PE pipes of different SDR.
EF Welding Machine
Electrofusion welding employs fittings to be placed around the PE pipe joints by means of welding. Metal coils are initially inserted into the fittings to be joined, and electric current is passed through the coil to generate heat and melt the pipes, forming a good bonding upon the setting of the welded joint as illustrated in fig. 1.
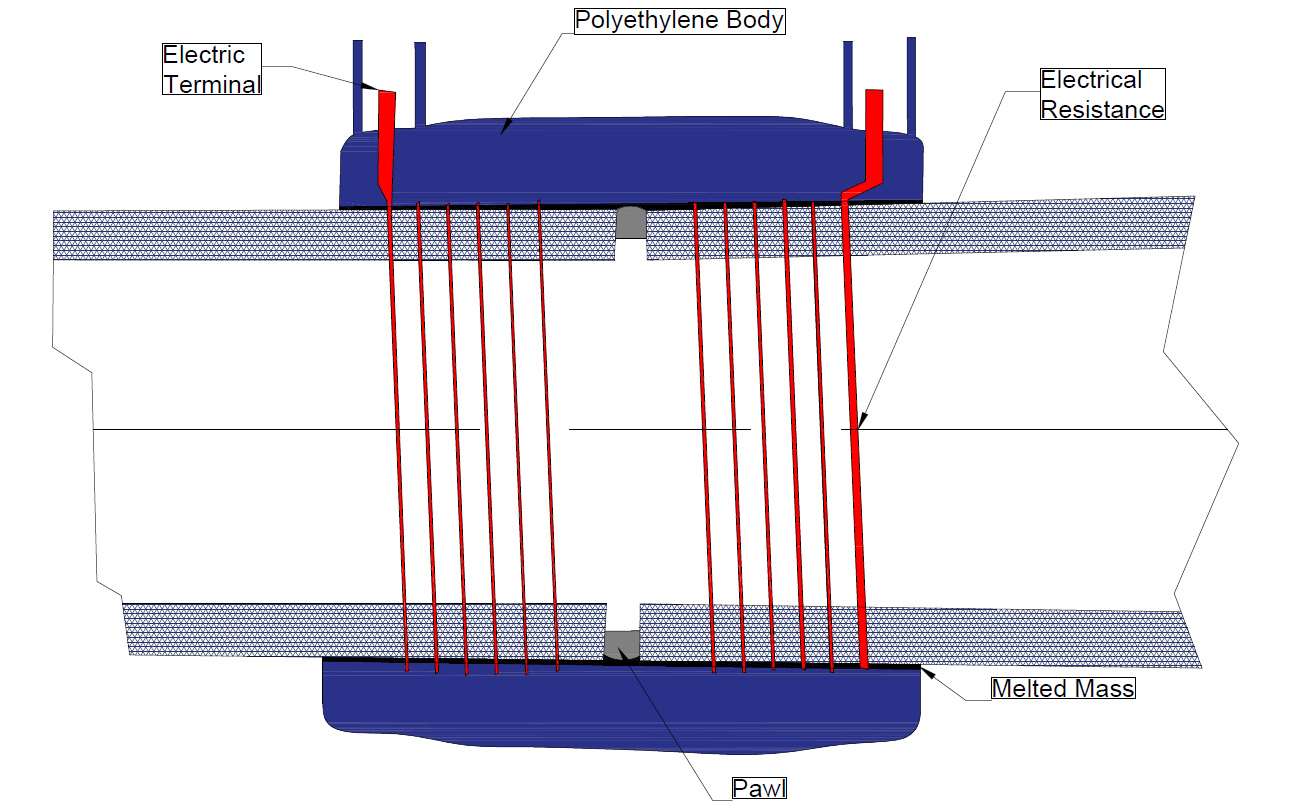
Fig. 1. EFW Setup
There are two possible fittings used in electrofusion welding viz. couplers and tapping tees or saddles. Coupler fittings require two sets of coils, which results in two distinct fusion zones during welding. The inner diameter of the coupler fitting is generally larger than the outer diameter of the pipes. This aids in increasing the ease of assembling and allow for minor inconsistencies in pipe diameter. Proper insertion of the pipes in the coupler is critical for the creation of a strong joint as inaccurate positioning can lead to the movement of the heating coils, which can lead to loss of polymer from the joint and reduction in the strength of the joint. The tapping tee joining method is rarely used but operates under the same principles as a coupler but requires additional clamping for ensuring a proper fit.
Types of EF Welding Machines
Manual EF welding is performed in line with dimensional tolerance and manufacturer guidelines related to the PE pipe and fittings to be welded together. The input data needed for welding [Refer to fig. 2] is entered manually into the control unit of the welding machine.
Automatic EF welding using a control unit with a barcode scanner ensures that the information is cent percent correct for the fittings and utilizes a fully automated input data entry. Control units operate with barcode-marked fittings in accordance with ISO 13950 standards, with a maximum output of 48 Volts.
Decoding the EF Barcode
A typical bar code for EF welding fittings is illustrated in fig. 2.
Fig. 2: A typical Barcode for EF Fittings.
- The first 8 digits represents the manufacturer's code.
- The digits 9 to 11 represents the dimension of the item in mm.
- The digits 13 & 14 indicates the EFW voltage in volts.
- The digits 16 to 18 represents the resistance in ohms.
- The digits 19 to 21 represents the fusion time needed for joining the fitting in seconds.
- The dimension (mm), voltage (V), fusion time (s), and cooling time (min) is indicated at the top of the barcode.
Comments (1)